Rheem is Changing the Waste Game
February 4, 2021
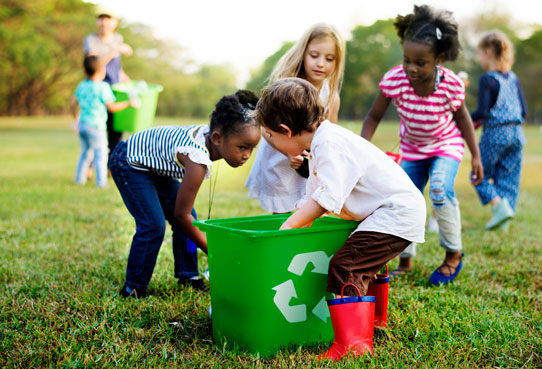
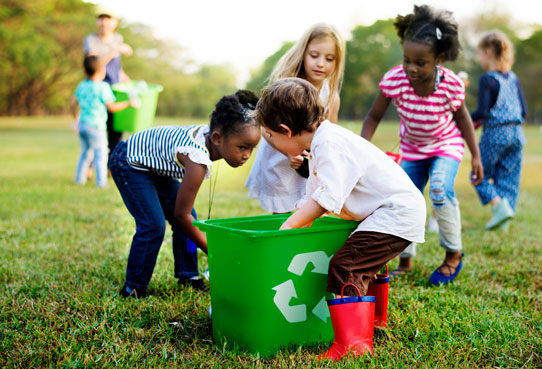
In 2019, Rheem formalized ambitious global goals; to reduce greenhouse gas emissions by 50%, achieve zero waste to landfill (ZWTL) in our manufacturing operations, and train 250,000 professionals on sustainable products and practices, all by 2025. These goals define our sustainability vision, A Greater Degree of Good™, in which we’ve committed to doing good by our customers, our partners, our employees and our planet.
ZWTL (or Go Zero! as we call it) is more than just a waste-reduction effort. It represents our drive toward operational excellence, which includes working smarter, consuming fewer resources and ensuring simpler, safer processes. It’s the kind of sustainability that offers good business value, and we believe that emphasizing efficiency and quality is an effective way to promote waste reduction.
“Sustainability is a by-product of being efficient and quality-conscious,” says Dan Partin, Manufacturing Engineering Manager at Rheem’s Fort Smith, Arkansas, facility. “You have to be responsible in manufacturing to achieve consistency. We put controls in place to get predicted outcomes of quality and efficiency. All we need is direction and support behind us to make our goals happen. Rheem gives us that support.”
Cliff Davis, Division Quality Systems Leader at Rheem’s Montgomery, Alabama, facility agrees. “Product quality plays a big role in waste-reduction. When you have products that are returned or have to be scrapped, you make more waste,” he says. “Every quality issue we solve is one less waste issue to deal with later on.”
From common sense to innovation
Our approach to waste reduction is common-sense: reduce, reuse, recycle and recover, but scaled to cover large facilities. Containers are placed where they’re needed most, with recycle bins and labeling in offices, cafeterias, halls, production floors and elsewhere as needed. Rheem also conducts Go Zero! educational campaigns and training to spark enthusiasm and maximize employee involvement.
Herlan Pedron, Operations Manager at the Eemax facility in Waterbury, Connecticut, explains that in manufacturing, the new philosophy is that waste should always be the last resort: “Use as much of any material as you can before throwing any of it away, and even then, check to see if anyone else can use what’s left.” Rheem already had programs to capture waste steel components, for example, but the company now collects even steel dust as part of its recycling efforts.
At some plants, innovation plays a major role. At our Rydalmere, Australia, facility, approximately 50% of the dried enamel waste is converted into a mist that can be used as an external enamel coating. The mist method is similar to the internal spray technique, where it is sprayed onto the external surface of cylinder as a thin coverage. This is a case of transforming previously non-recyclable landfilled waste, into re-usable material that prevents the external corrosion of cylinders and the need for frequent furnace cleaning due to scaling.
Similarly, a previously difficult oily sludge waste stream is now at the late trial stage of a dewatering process, and the residue is repurposed as a soil additive for composting—a case of transforming waste into material that promotes natural biological processes. Innovative technologies like these have the potential to catalyze industry-wide change in how waste is handled (and perceived) in heavy manufacturing.
Results and progress by the numbers
Go Zero! began at Fort Smith, followed by Montgomery, which together serve as a model for the rollout to the rest of North America and then to the world. Fort Smith has already achieved 90% diversion (away from landfill) and is on a fast track to 93% expected within a few months. (ZWTL is defined as at least 97% diversion.) Montgomery has achieved 71% diversion, with plans in place for 90% expected soon. Three facilities in Mexico (one in Mexicali and the WH NL and AC 28 plants in Nuevo Laredo) have already reached the ZWTL target. The AC 52 plant in Nuevo Laredo has reached 94%, and Rydalmere and our Raypak facility are both at 83%. By the end of 2021, all manufacturing plants are expected to have their diversion rates established and their own Go Zero! programs underway. Recycling centers are planned for all global sites by mid 2022.
Waste monitoring and auditing, conducted with help from a third-party provider, are important parts of making sure facilities maintain progress and will continue and expand until all sites are certified by 2025. “Waste audits tell us what our waste streams are, our current diversion rates and where we have the opportunity to make improvements,” explains Sara Corbett, Senior Manager for Brand Strategy at Rheem. “They take us to that next step of what a sustainability implementation plan can be.” And, she adds, “It is such an honor to be involved in sustainability, which has really become part of the fabric of Rheem.”
The social benefits of zero waste
Our ZWTL efforts are good for the planet, but they have benefits closer to home too. The rollout of Go Zero! has been popular internally as employees take satisfaction in doing a better job, building better products and reducing environmental impact. Everyone is encouraged to identify areas for efficiency and waste reduction that our experts and auditors may overlook.
Domingo Mohedano, Director of Operations at the HTPG facility in Scottsboro, Alabama, says, “Our employees are eager to see how we as leaders are taking on this initiative to make a difference for the environment, for future generations and for our local community.”
Programs like this also make Rheem more attractive to job candidates, who increasingly expect forward-thinking companies to take environmental issues seriously. “I personally like knowing that we’re part of the sustainability effort and that we’re being smart about creating a better future,” says Tracy Bennett, Store Development Manager at Rheem’s Randleman, North Carolina, facility. “We’re thinking more globally, not just about profit. This is a great opportunity to learn things we can do to help right now and be a part of long-term planning as well.”
Mark Evans, Vice President and General Manager of HTPG, adds, “Every day we come to work and try to make people’s lives better with the products we develop, but this is an opportunity for us to also build into our plant and into our processes results that do no harm to the environment.”
Creating a culture of environmental awareness
Only three years ago, few Rheem employees would have described sustainability as part of the company’s fabric. Now, nearly all of them would. As part of A Greater Degree of Good, ZWTL is both a product and a driver of a complete transformation of Rheem culture. As Kimberly Markey, Marketing Manager at our Eemax facility in Waterbury puts it, “Everyone here realizes we have to do good things for our planet in order for it to be a thriving place for our children’s future.” And that is what A Greater Degree of Good is all about.